Ever since we moved in we'd talked about putting a fountain in the "grotto" in the wall at the back of the property.
A couple of years after we moved in and had been doing a lot of work, we were at a party and met a local architect who is regarded as an expert on Cass Gilbert houses. He mentioned that he liked our renovation work and that he previously had lived in the house immediately behind ours (see the red garage in the first photo). He said that there indeed had been a fountain in the grotto years ago. He had rented out the second floor of his house to some college students and when they eventually moved out, they left behind what he believed was the original fountainhead from our fountain. He had it at his second home an hour or so away and would be willing to return it to us. Though we've worked with him on Cass Gilbert Society functions several times since, we never got it from him. I'm not certain he recalls the offer due to various other circumstances, so we had to make alternate plans.
The grotto had a bunch of dirt and decomposed material in it. In addition, SWMBO had been dumping our old potting soil in there. So the first step was to dig all that out. I discovered that at the bottom there was an old layer of concrete. It was cracked in several places and was uneven. In addition, the stones surrounding the basin had shifted over time and had large gaps between them, so there was no way to make it water tight.
Another solution needed to be found. Much internet searching and measuring followed before I found the solution; a pond-less water basin.
But on the bright side, the grotto contained a cool block of stone with a fountain carved into its face (see previous photo)...
The first step was to move that block of stone. Little Man (who is now a collegiate offensive lineman and is bigger than me) and I "rolled" it out and onto the ground to the left of the grotto. We later determined that it probably weighs 325+ pounds given that limestone weighs about 150 pounds per cubic foot.
Then I leveled the bottom with a layer of "paver base". Basically paver base is sharp sand and small aggregate that compacts well to provide a solid and level base.
It didn't take long for the basin to arrive. Due to its size it comes on its own pallet and is shipped by truck rather than by USPS, Fedex, etc. For reference, this basin is 36 inches in diameter, 16 inches high, weighs about 40 pounds, and holds about 60 gallons of water. There are several internal pillars and a central column that support the grate and up to 750 pounds of static load (whatever you use as the fountainhead). The pump can be accessed through the pump cover (the white plate on the left side of the grate).
Once it was level, I filled it halfway with water so that it wouldn't shift while I put topsoil around the exterior of the basin.
Our mason, Dave, stopped by Thursday to drill the hole in the stone block. It is a 1-inch hole that goes straight down through the block, centered about a third of the way back from the front edge. That evening, Little Man and I moved the block into place (did I say it weighs over 325 pounds?) and ran 1-inch vinyl tubing from the pump and up the full length of the hole. I had to make some adjustments to get the proper flow rate and to get the tubing to route properly without kinking. A 90-degree elbow connected to the pump outlet, a valve to control the flow, and barbed fitting for the tubing were all that was needed. I also needed to cut a little of the lip of the grate away to be able to get the pump cord in and out easily. Because it will get damaged if it is allowed to freeze, the pump needs to be removed for the winter.
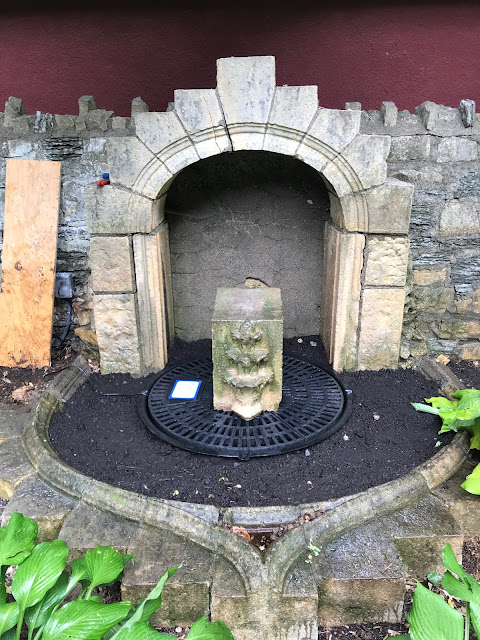
SWMBO gave me "permission" to select the stone that covers the grate. We'd had some discussion about going to a local landscape center, but I wasn't convinced we could find something with stones in the Goldilocks zone: not too big, but not so small they fell through the grate. I didn't think that river rock would look right. We had a couple of extra limestone blocks laying about, so I grabbed great-grandpa Joe's stone mason tools and went to work breaking stone into the proper sized pieces. It took me a good part of the afternoon...
Saturday I added a bit more soil and transplanted some perennials to soften the edges and camouflage the pump cord, etc. In the back are variegated hosta. Along the sides are Japanese painted fern. We plan to put annuals with a pop of color along the curve in front.
Lastly, the fountain in action: